Researchers at Samara University have become the first to “print” one of the most critical elements of a small-size gas-turbine engine – the combustion chamber – from powdered metal using a selective laser melting unit – the SLM280.
The work was done at the Additive Technologies Laboratory of Samara University’s Institute for Engines and Propulsion Systems.
The bench tests, conducted in conjunction with the university’s academic center for gas-dynamics research, showed that the combustion-chamber prototype fabricated using the breakthrough technology fully conforms to all of the required specifications. The material and the chamber itself successfully withstood all of the necessary stressors, both in terms of prolonged thermal load (up to 1.5 hours), as well as follow-up short-term load (startup-setup for 10 minutes).
“The prototype was tested on the test-firing bench for duration of operation in operating conditions that closely approximate the real-world environment. The entrance to the chamber was supplied with air heated to a temperature of 400˚ Celsius – the working temperature of air at the entrance to the combustion chamber of a gas-turbine engine. Combustion conditions were designed to approximate real-world conditions as closely as possible. The temperature of the working medium in the primary zone of the combustion chamber was 1600˚ C, while at the exit from the CC, the temperature of combustion residue amounted to 1200˚ C,” explained the Director of Samara University’s Academic Center for Gas-Dynamics Research, Mikhail Anisimov.
The chamber was completely fabricated using domestically-produced powdered metal. In order to ensure that the desired result would be achieved, the researchers used it to “grow” more than a hundred trial specimens – metal blanks melted in different sintering modes to determine the strength properties of the metal.
The combustion chamber is one of the critical elements of the small-size gas-turbine engine (SGTE) being built at Samara University using the additive technologies method. Using standard (traditional) technologies, fabricating a similar chamber would take half a year. What’s more, under the traditional approach, getting such a chamber to reach maximum operating characteristics would take about five years.
Applying these same additive technologies makes it possible to fabricate intricately-shaped parts in a short amount of time, without using machining attachments. These factors allow for a drastic curtailment of the part-production cycle, as compared to the longer cycle entailed by traditional methods.
The technology incorporated in selective laser melting (SLM) uses a high-powered laser to melt a fine layer of the powdered metal according to the 3D model. The primary materials used in fabricating gas-turbine engines according to the SLM method are high-tensile steel, titanium alloys and nickel-based alloys.
The successful fabrication of a working combustion chamber using the additive-technologies method opens the way for the university’s researchers to create a full gas-turbine engine in the near future.
“The first SGTE trial prototype created at Samara University using the additive-technologies method could appear in as little as half a year. Moving forward, this method will be used in the mass production of parts on 3D printers, which will dramatically reduce the time needed for subsequent work on engine production,” insists the Head of the Additive Technologies Laboratory at Samara University, Vitaliy Smelov.
Today, researchers from Samara University, in partnership with the St. Petersburg Polytechnic University, are busy developing a Russian-made 3D laser unit that will make it possible to utilize the technology developed at Samara University to manufacture “grown-up” gas-turbine and aircraft engines at production facilities.
What’s more, in conjunction with Progress State Research and Production Space Center, specialists from Samara University have begun implementing a project involving the creation of parts for the aerospace industry on the basis of additive technologies.
Photo: Ekaterina Vinokurova (“Illuminator “photography club)
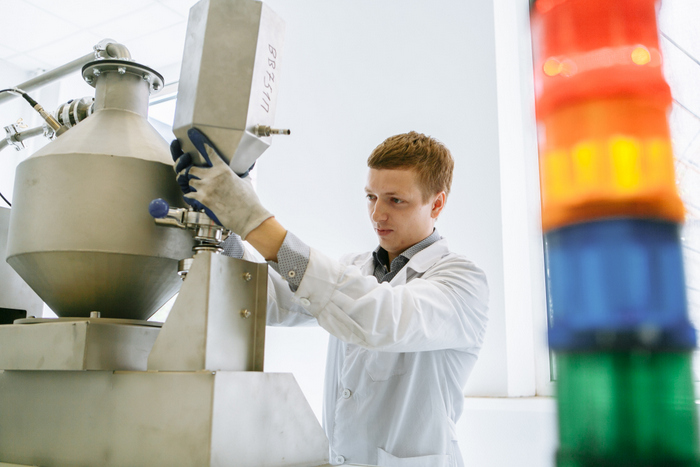
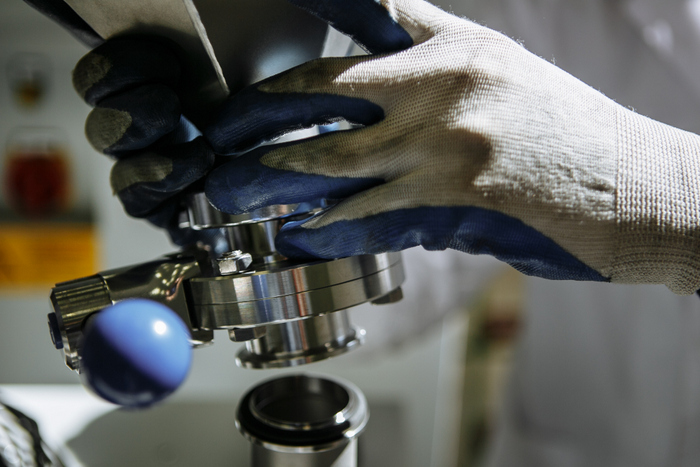
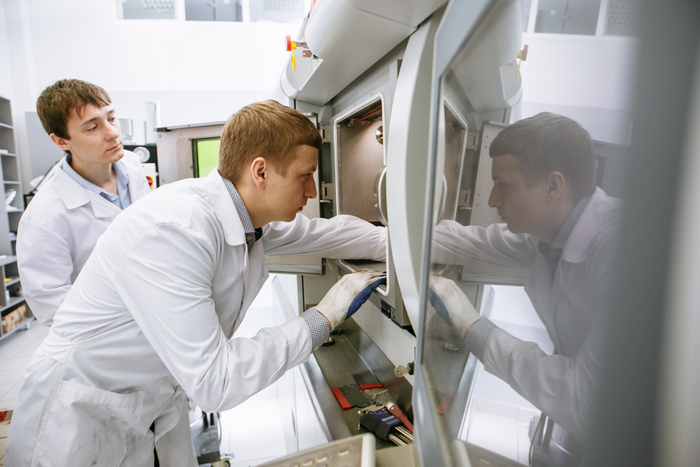
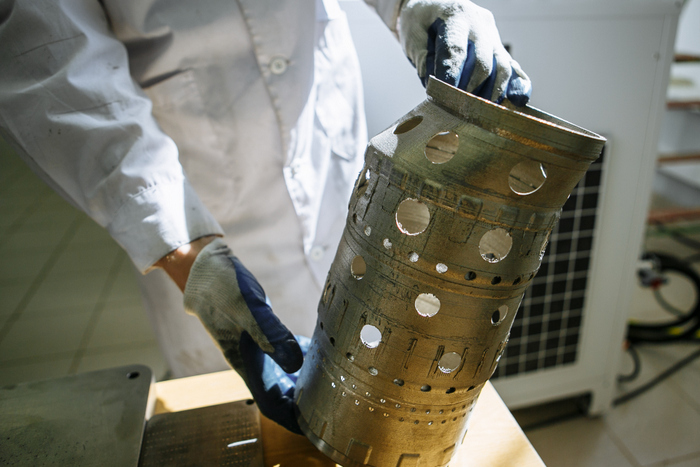